Etimologia:
Da palavra Automation (1960), buscava enfatizar a participação do computador no controle automático industrial.
Definição atual:
“Qualquer sistema, apoiado em computadores, que substitui o trabalho humano, em favor da segurança das pessoas, da qualidade dos produtos, rapidez da produção ou da redução de custos, assim aperfeiçoando os complexos objetivos das indústrias, dos serviços ou bem estar” (Moraes e Castrucci, 2007).
A automação nas atividades humanas
Criada para facilitar a realização das mais diversas atividades humanas, a automação pode ser observada:
Nas residências : nas lavadoras de roupas e de louças automáticas; nos microondas; nos controles remotos de portões de garagem, etc.
Na rua: nos caixas de bancos automáticos; nos controladores de velocidades de automovóeis; nos trens do metrô; nos cartões de crédito, etc.
No trabalho: nos registradores de ponto automático; nos robôs industriais; no recebimento de matéria-prima através de um sistema automático de transporte de carga; na armazenagem do produto final num depósito automatizado; no controle de qualidade através de sistemas de medição e aferição; no controle de temperatura ambiente ou de uma coluna de fracionamento de petróleo; nos sistemas de combate à incêndios, etc.
No lazer: em máquinas automáticas de refrigerantes ; em esteiras automáticas de academia; nos aparelhos de reprodução de vídeo ou DVD players; nos videogames, etc.
A automação no meio produtivo
“O processo industrial constitui-se na aplicação do trabalho e do capital para transformar a matéria-prima em bens de produção e consumo, por meios e técnicas de controle, obtendo valor agregado ao produto, atingindo o objetivo do negócio”.
Processo Industrial Contínuo: Quando a maioria das variáveis de controle é manipulada na forma contínua, ou analógica. (Indústria Química, farmacêutica...)
Processo Industrial Discreto: Quando a maioria das variáveis de controle é manipulada na forma discreta ou digital.
Características e conceitos da automação industrial
“A Automação é um conceito e um conjunto de técnicas por meio das quais se constroem sistemas ativos capazes de atuar com eficiência ótima pelo uso de informações recebidas do meio sobre o qual atuam.”
Na Automação Industrial se reúnem três grandes áreas da engenharia:
1. A mecânica, através das máquinas que possibilitam transformar matérias primas em produtos “acabados”.
2. A engenharia elétrica que disponibiliza os motores, seus acionamentos e a eletrônica indispensável para o controle e automação das malhas de produção;
3. A informática que através das arquiteturas de bancos de dados e redes de comunicação permitem disponibilizar as informações a todos os níveis de uma empresa.
Assim, a automação, tão presente nas atividades humanas, está presente também nos processos industriais, com o mesmo objetivo básico, que é facilitar os processos produtivos, permitindo produzir bens com :
• menor custo;
• maior quantidade;
• menor tempo;
• maior qualidade.
• maior quantidade;
• menor tempo;
• maior qualidade.
Olhando por este aspecto, vemos que a automação está intimamente ligada aos sistemas de qualidade, pois é ela que garante a manutenção de uma produção sempre com as mesmas características e com alta produtividade, visando atender o cliente num menor prazo, com preço competitivo e com um produto de qualidade.
Pensando no meio ambiente, observa-se também que a automação pode garantir o cumprimento das novas normas ambientais, através de sistemas de controle de efluentes (líquidos que sobram de um processo industrial), emissão de gases, possibilidade de uso de materiais limpos, reciclagem, etc.
Portanto, a automação tem papel de muita importância na sobrevivência das indústrias, pois garante a melhoria do processo produtivo e possibilita a competição nesse mercado globalizado, onde o concorrente mais próximo pode estar do outro lado do mundo.
Componentes básicos da automação
Sistemas automatizados são, algumas vezes, extremamente complexos, porém, ao observar suas partes nota-se que seus subsistemas possuem características comuns e de simples entendimento. Assim, formalmente, um sistema automatizado possui os seguintes componentes básicos:
• sensoriamento(sensores);
• comparação e controle (Controlador e PLC;
• comparação e controle (Controlador e PLC;
• actuação (Servomotores, motores, actuadores,etc).
Exemplo 1 - Um aquário e a temperatura de sua água.
Num aquário deve-se manter a água em torno da temperatura ambiente (25°C). Não é necessário ser muito rigoroso sendo que a temperatura pode variar de 23 a 28°C.
Nota-se que a temperatura da água pode variar e deve ser ajustada de acordo com a necessidade.
Considere o esquema a seguir:
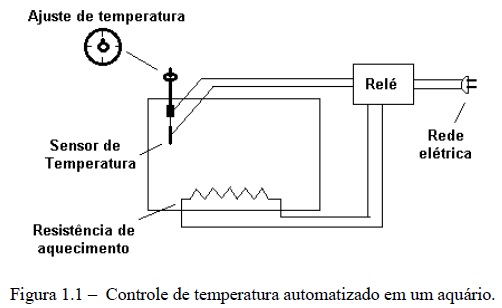
Neste exemplo podem ser identificados os componentes básicos da automação (processo, sensor, atuador, controle e distúrbio):
- O processo (aquário), que requer o controle da temperatura.
- O sensor de temperatura, constituído pelo termômetro de mercúrio;
- O controlador, estabelecido pelo acoplamento de um sistema mecânico de ajuste ao termômetro. Este sistema mecânico movimenta um contato metálico ao longo do corpo do termômetro. Ele permite ao controlador, fazer uma comparação com um valor pré-ajustado (ponto de ajuste) e tomar a decisão de ligar ou desligar o atuador (resistência), mantendo a temperatura dentro de um limite considerado aceitável.
- O distúrbio é representado pelas condições externas que podem influenciar na temperatura da água. A temperatura do ambiente externo influencia diretamente no controle, determinando uma condição diferente de atuação no processo.
- O atuador formado pelo relé elétrico e a resistência. Quando o deslocamento do mercúrio alcança o ponto de ajuste, um contato elétrico é fechado, sendo ele ligado ao relé que, usando a alimentação da rede, desliga a resistência responsável pelo aquecimento da água. Então, em forma de diagrama, nesse sistema temos:
- O sensor de temperatura, constituído pelo termômetro de mercúrio;
- O controlador, estabelecido pelo acoplamento de um sistema mecânico de ajuste ao termômetro. Este sistema mecânico movimenta um contato metálico ao longo do corpo do termômetro. Ele permite ao controlador, fazer uma comparação com um valor pré-ajustado (ponto de ajuste) e tomar a decisão de ligar ou desligar o atuador (resistência), mantendo a temperatura dentro de um limite considerado aceitável.
- O distúrbio é representado pelas condições externas que podem influenciar na temperatura da água. A temperatura do ambiente externo influencia diretamente no controle, determinando uma condição diferente de atuação no processo.
- O atuador formado pelo relé elétrico e a resistência. Quando o deslocamento do mercúrio alcança o ponto de ajuste, um contato elétrico é fechado, sendo ele ligado ao relé que, usando a alimentação da rede, desliga a resistência responsável pelo aquecimento da água. Então, em forma de diagrama, nesse sistema temos:
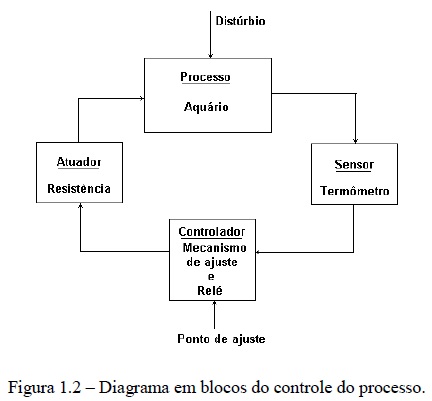
Observa-se que existe uma influência da ação de aquecimento da água no valor medido pelo sensor de temperatura. Este ciclo fechado é chamado de malha fechada de controle, ou sistema de realimentação, no qual a saída do sistema influencia diretamente na situação de sua entrada.
Em alguns processos, não existe a realimentação, isto é, a ação do atuador comandada pelo controlador não é observada por um sensor que realimenta o sistema. Um exemplo típico é o de uma máquina de lavar roupa, que por não possuir um sensor de roupa limpa, funciona em um ciclo aberto de controle, chamado de malha aberta.
O controle apresentado neste exemplo não possui precisão, isto é, nada garante que a temperatura permaneça exatamente no ponto ajustado, ou que fique oscilando em torno do valor ajustado. Este tipo de controle é chamado de Liga/Desliga (ou ON/OFF). O atuador (resistência) permanece em dois estados bem definidos (nenhuma corrente = desligado e máxima corrente = ligado). É considerado então um controle descontínuo.
A quantidade de informações e conceitos que podem ser retirados de um sistema tão simples como esse é muito grande, sendo que elas resumem os conhecimentos necessários para o entendimento de um sistema automatizado.
Exemplo 2 - Um tanque de combustível e seu nível.
Neste caso, pode-se abordar duas situações de controle automatizado:
Medição descontínua: para garantir segurança evitando o transbordamento ou esvaziamento abaixo de determinada posição mínima.
A medição descontínua normalmente é feita por sensores do tipo chave com dois estados, ativo ou não ativo. Considerando um contato elétrico, esse poderá estar aberto (possibilitando passagem de corrente) ou fechado (impedindo a passagem de corrente).
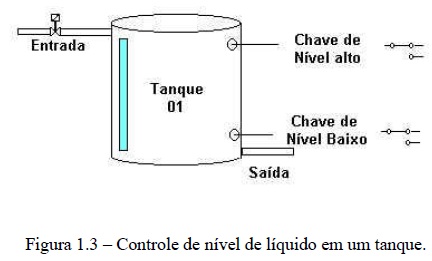
Medição contínua: para determinar a quantidade de combustível armazenado.
Além do sistema de segurança mostrado anteriormente, tem-se a necessidade de determinar a quantidade armazenada de um certo combustível dentro deste tanque. Nesse caso é necessário empregar um medidor que "observe" continuamente as variações da altura da coluna líquida no interior do tanque. Este medidor deve fornecer um sinal de saída contínuo, proporcional à altura do tanque.
Tendo o valor da altura dada pelo medidor e conhecendo a capacidade do tanque dada pelo formato do próprio tanque, é possível calcular a quantidade de combustível do tanque para cada condição de nível.
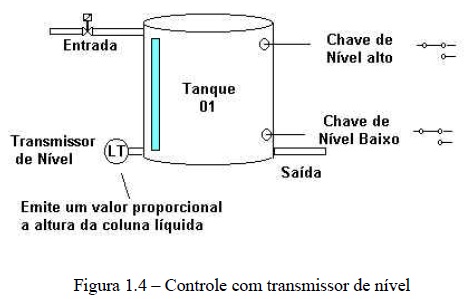
Observando os exemplos acima, conclui-se que é possível ter sensores descontínuos (Liga/Desliga) e contínuos (chamados analógicos). A escolha do tipo de medição vai depender do que se pretende na automação. No caso do tanque, os dois controles podem estar presentes, cada um cuidando de sua parte no controle do sistema como um todo.
Tipos de sistemas de sistemas de processos industriais
Em automação tem se tornado necessário classificar os sistemas em função de suas ocorrências mais comuns e importância. Além dos sistemas dinâmicos acionados pelo tempo, exemplo típico dos fenômenos químicos, físicos, térmicos, regidos por equações diferenciais, também aparecem em grande quantidade os sistemas de chaveamento manual, automático, as manufaturas, as filas de serviços, etc, que são acionados por eventos, e não são regidos por equações diferenciais. Estes últimos são conhecidos como sistemas dinâmicos a eventos discretos (SED’s) e são sistemas cuja evolução decorre unicamente de eventos instantâneos, repetitivos ou esporádicos.
Tipos de controle na automação
Pode-se classificar o controle em dois grandes grupos:
Controle Dinâmico
O controle dinâmico procura estabelecer o comportamento estático e dinâmico dos sistemas físicos, tornando-os mais obedientes aos operadores e mais imunes às perturbações dentro de certos limites.
Utiliza medidas das saídas do sistema a fim de melhorar o seu desempenho operacional, através de realimentação.
Possui um incalculável poder tecnológico, permitindo o aperfeiçoamento de processos, aumento de velocidade e precisão.
É característico da automação industrial de controle de processos (automação contínua), sendo tradicionalmente empregado o controle do tipo P + I + D (proporcional + integral + derivativo), entre outras escolhas.
Exemplo de aplicação: controle de temperatura de um aquário.
Controle Lógico ou Controle de Eventos
O Controle lógico complementa os sistemas lógicos permitindo que eles respondam a eventos externos ou internos de acordo com novas regras que são desejáveis de um ponto de vista utilitário.
Utiliza sinais sempre discretos em amplitude, geralmente binários e operações não-lineares e se apresenta na forma de circuitos (elétricos, hidráulicos, pneumáticos, etc) de redes lógicas combinatórias (sem memórias ou temporizações) cujos projetos são construídos com álgebra booleana (descreve, analisa e simplifica as redes com auxílio de Tabelas da Verdade e Diagramas de relés) ou em redes sequenciais (com memória, temporizadores e entrada de sinais em instantes aleatórios) cujo projeto utiliza a teoria dos autômatos finitos, redes de Petri, cadeias de Markov ou em simulações por computador.
É característico da automação industrial de manufatura (automação discreta).
Exemplo de aplicação: botões de segurança de uma prensa de alavanca.
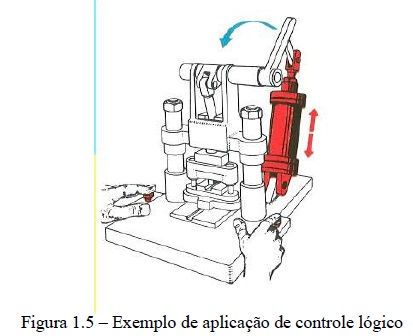
Os dois tipos de controle (dinâmico e lógico) são empregados em proporções extremamente variáveis, conforme o processo, e misturam-se nos controladores lógicos programáveis (CLPs) e PCs.
No entanto, as teorias do controle dinâmico e do controle lógico desenvolvem-se independentes uma da outra. O controle dinâmico busca evitar a instabilidade do sistema, enquanto o controle lógico procura evitar o conflito ou a parada total da evolução dos sinais.
Aspectos gerais da automação
A automação resulta de diversas necessidades da indústria: maior nível de qualidade dos produtos, maior flexibilidade de modelos para o mercado, menores custos e perdas de materiais e de energia, mais disponibilidade e qualidade da informação sobre o processo e melhor planejamento e controle da produção.
Segundo o grau de complexidade e meios de realização física, a automação industrial pode ser classificada em:
• Automações especializadas (menor complexidade)
• Grandes sistemas de automação (maior complexidade)
• Automações Industriais de âmbito local (média complexidade)
• Grandes sistemas de automação (maior complexidade)
• Automações Industriais de âmbito local (média complexidade)
Automações especializadas (menor complexidade)
Emprega microprocessadores com programação normalmente em linguagem de máquina e memórias do tipo ROM.
Ex.: automação interna aos aparelhos eletrônicos, telefones, eletrodomésticos, automóveis.
Grandes sistemas de automação (maior complexidade)
Utiliza programação comercial e científica em software de tempo real.
Ex.: Controladores de vôos nos aeroportos, controle metroviário, sistemas militares.
Automações Industriais e de serviços de âmbito local (média complexidade)
Baseia-se no uso dos CLP’s isolados ou em redes.
Ex.: Transportadores, processos químicos, térmicos, gerenciadores de energia e de edifícios.
Corresponde à grande maioria das aplicações existentes, sendo este o foco do curso.
Arquitetura da automação industrial
A Figura 1.6 mostra os níveis hierárquicos de um processo de automação industrial, representado pela conhecida Pirâmide de Automação.
Para cada nível está associado um formato de comunicação de dados que pode diferir daquele adotado para a comunicação entre níveis.
Na base da pirâmide aparece o Controlador Lógico Programável, responsável por acionar as máquinas, motores e outros processos produtivos.
No topo da pirâmide, destaca-se a informatização ligada ao setor corporativo da empresa.
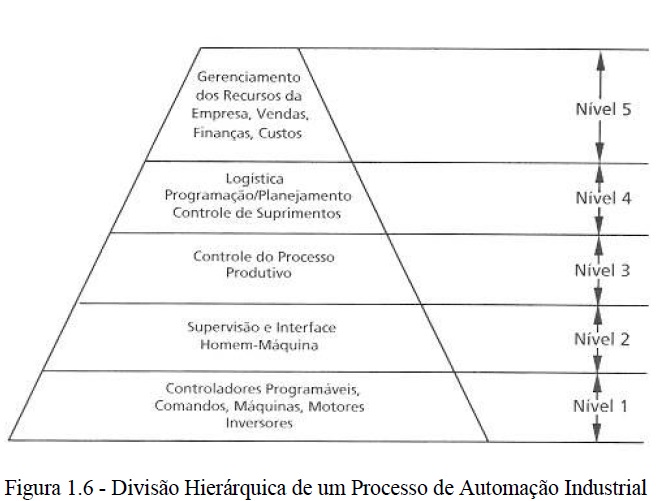
Nível 1: Chão de fábrica (Máquinas, dispositivos e componentes)
Na base da pirâmide tem-se o nível responsável pelas ligações físicas da rede ou o nível de E/S. Neste nível encontram-se os sensores discretos, as bombas, as válvulas, os contatores, os CLPs e os blocos de E/S. O principal objetivo é o de transferir dados entre o processo e o sistema de controle. Estes dados podem ser binários ou analógicos e a comunicação pode ser feita horizontalmente (entre os dispositivos de campo) e verticalmente, em direção ao nível superior. É neste nível, comumente referenciado como chão de fábrica, que as redes industriais têm provocado grandes revoluções.
Ex.: linha de montagem e máquina de embalagens.
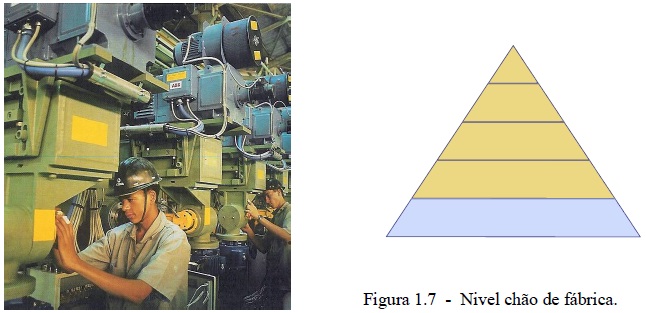
Nível 2: Supervisão e Controle (IHMs)
É o nível dos controladores digitais, dinâmicos e lógicos e de algum tipo de supervisão associada ao processo.
Concentra as informações sobre o nível 1.
Ex.: Sala de supervisão.
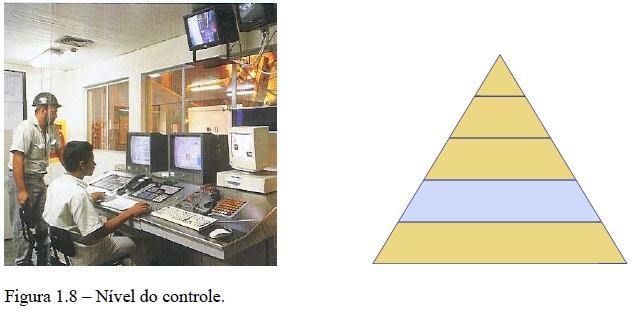
Nível 3: Controle do Processo Produtivo
Permite o controle da planta, sendo constituído por bancos de dados com informações dos índices de qualidade da produção, relatórios e estatísticas de processo, índices de produtividade e etc.
Ex.: avaliação e controle da qualidade em processo alimentício e supervisão de laminadores.
Nível 4: Controle e Logística dos Suprimentos
É o nível responsável pela programação e pelo planejamento da produção.
Ex.: controle de suprimentos e estoques em função da sazonalidade.
Nível 5: Gerenciamento Corporativo
É o nível responsável pela administração dos recursos da empresa.
Do ponto de vista da comunicação das informações, no topo da pirâmide encontrase o nível de informação da rede (gerenciamento). Este nível é gerenciado por um computador central que processa o escalonamento da produção da planta e permite operações de monitoramento estatístico da planta sendo implementado, na sua maioria, por softwares gerenciais/corporativos.
No nível imediatamente abaixo, localiza-se a rede central, a qual incorpora os DCSs (Sistemas de Controle Discreto) e PCs. A informação trafega em tempo real para garantir a atualização dos dados nos softwares que realizam a supervisão da aplicação.
Uma das dificuldades dos primeiros processos de automação industrial baseava-se no “ilhamento” das informações dentro do seu respectivo nível da pirâmide. Poucas informações fluíam do nível de supervisão e controle para o nível de controle discreto e praticamente nenhuma informação fluía para o topo da pirâmide, onde se encontram os softwares de gerenciamento da empresa. Nos projetos de automação modernos as informações fluem entre todas as camadas. Esta característica é tão importante para as indústrias, hoje em dia, que muitas delas estão atualizando suas plantas industriais, ou incorporando novas tecnologias em sistemas antigos (conhecido por RETROFIT).
A visão crítica ao automatizar processos
As principais motivações para a automação de um processo industrial são a redução do custo, a melhoria da qualidade do produto e a realização de tarefas que são danosas ao ser humano (tarefas repetitivas ou que exigem grande esforço físico, ambientes perigosos ou insalubres). Quase sempre os dois primeiros motivos são os que movem os processos de automação.
A automação é capaz de manter o homem no domínio da situação no que se refere à produção industrial, porém numa posição mais confortável.
O homem, nessa situação, necessita cada vez mais usar o seu cérebro e cada vez menos seus músculos. Porém essa mudança faz com que os profissionais necessitem cada vez mais se especializar, buscando competências para o desenvolvimento de suas atividades. A reconversão, isto é, a adaptação a novos postos de trabalho e a qualificação profissional são condições primordiais.
Embora a automação seja um processo irreversível na sociedade e o fator custo X benefício, calcado no aumento do lucro das empresas, o grande definidor do emprego da tecnologia, é fundamental que empresários e engenheiros tenham uma visão das consequências sociais que um processo de automação pode trazer:
• A automação quase sempre gera desemprego;
• A automação requer um profissional cada vez mais qualificado;
• A automação requer um profissional cada vez mais qualificado;
Em países em desenvolvimento o governo não possui uma infra-estrutura para atender a população desfavorecida.
O “sonho” propalado da automação era que ela traria melhor qualidade de vida para toda a sociedade, reduzindo a carga horária de trabalho para possibilitar ao ser humano um convívio mais harmonioso entre si e a natureza. Este sonho tem se esbarrado na boca voraz do capitalismo selvagem que infelizmente, sem a força de um governo forte, é incapaz de dividir as riquezas acumuladas para o bem de toda a sociedade.
O papel de preparar esse novo profissional é das escolas que deve contar com o apoio das indústrias, porém com a velocidade que ocorrem as mudanças tecnológicas, não é permitido ao profissional estar sempre num ambiente escolar para sua preparação. Então, o que fazer?
A conclusão que se chega é que o profissional cada vez mais terá que se autodesenvolver, provendo o seu próprio conhecimento, não só na área tecnológica, mas também em outras áreas, de modo mais amplo, como: economia, sociologia, comércio exterior, qualidade, relações humanas, meio ambiente, etc.
Cabe ao engenheiro e aos empresários a visão crítica diante dos processos de automação. Mais importante do que retardar um processo inevitável talvez seja criar condições para que o bem final possa ser melhor repartido entre todos.
Tendências da automação
Tecnologia Wireless: de lenta, cara e insegura tornou-se mais rápida e econômica. Chips de menor capacidade residirão inteligência diretamente em sensores e atuadores – softwares serão parte do produto.
Controles baseados em PLC ou PC serão obsoletos e caros.
A propriedade da solução tecnológica será medida em meses em vez de anos Sistemas microeletromecânicos serão usados para miniaturizar sensores, atuadores, motores, engrenagens displays para equipamentos digitais.
0 comentários:
Enviar um comentário